Different elements have different functions and effects in the manganese steel casting wear parts.
Carbon Element. Carbon is one of the two most important elements in manganese steels along with manganese. Manganese steels are a supersaturated solution of carbon. For most standard manganese steel grades the carbon and manganese are in an approximate ratio of Mn/C=10. These steels, therefore, are typically 12% Mn and 1.2% C. This ratio was mainly set up by early steel-making limitations and the fixed ratio has no real significance. Increasing the carbon content raises the yield strength and lowers the ductility. See the following picture for the effects of increasing carbon content on the properties of 13% manganese steel.
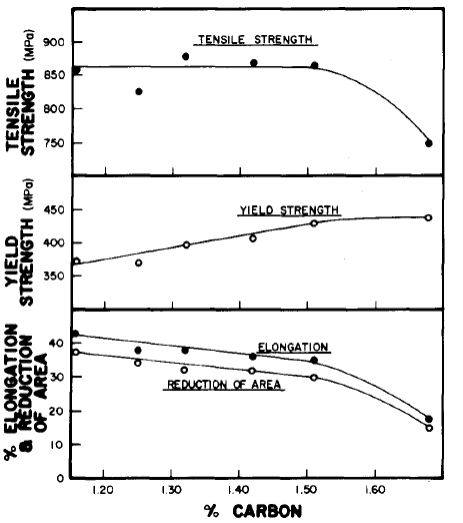
Effect of carbon upon the tensile properties of manganese steel
Most manganese steels are used in gouging abrasion and high impact wear situations so manufacturers try to maximize carbon contents. Practical limits do exist and as the carbon content exceeds 1.3% cracking and undissolved grain boundary carbides become more prevalent. The premium grades of manganese steels, those with high manganese contents, have pushed the upper carbon limit well beyond 1.3%.
Manganese Element. Manganese is an austenite stabilizer and makes this family of alloys possible. It decreases the austenite to ferrite transformation temperature and therefore helps to retain a fully austenitic structure at room temperature. Alloys with 13% Mn and 1.1% C have martensite start temperatures below -328°F. The lower limit for manganese content in plain austenitic manganese steel is near 10%. Increasing manganese levels tend to increase the solubility of nitrogen and hydrogen in the steel. Premium alloys with higher carbon contents and additional alloy elements exist with manganese levels from 16-25% manganese. These alloys are proprietary to their manufacturer.
Silicone Element. The specification content of silicon in high manganese steel is 0.3% ~ 0.8%. Silicon will reduce the solubility of carbon in austenite, promote carbide precipitation, and reduce the wear resistance and impact toughness of steel. Therefore, the silicon content should be controlled at the lower specification limit.
Phosphorus Element. The specification content of high manganese steel is P ≤ 0.7%. When smelting high manganese steel, because of the high phosphorus content in ferromanganese, the phosphorus content in steel is generally high. Because phosphorus will reduce the impact toughness of steel and make the casting easy to crack, the phosphorus content of steel should be reduced as much as possible.
Sulphur Element. The specification of high manganese steel requires S ≤ 0.05%. Due to the high manganese content, most of the sulfur and manganese in the steel combine with each other to form manganese sulfide (MNS) and enter the slag. Therefore, the sulfur content in the steel is often low (generally no more than 0.03%). Therefore, the harmful effect of sulfur in high manganese steel is higher than that of phosphorus.
Chromium Element. Chromium is used to increase the tensile strength and flow resistance of manganese steels. Additions of up to 3.0% are often used. Chromium increases the solution-annealed hardness and decreases the toughness of the manganese steel. Chromium does not increase the maximum work-hardened hardness level or the strain hardening rate. Chromium bearing grades require higher heat treatment temperatures as chromium carbides are more difficult to dissolve into solution. In some applications, chromium can be beneficial, but in many applications, there is no benefit to adding chromium to manganese steel.
Molybdenum Element. Molybdenum additions to manganese steels result in several changes. First, the martensite starts temperature is lowered which further stabilizes the austenite and retards carbide precipitation. Next, molybdenum additions change the morphology of the carbides that form during reheating after the material has had a solution treatment. Grain boundary films of acicular carbides typically form, but after adding molybdenum the carbides that precipitate are coalesced and dispersed through the grains. The result of these changes is that the toughness of the steel is improved by the addition of molybdenum. Another benefit of molybdenum additions can be improved as-cast mechanical properties. This can be a real benefit during casting production. In higher carbon grades molybdenum will increase the tendency for incipient fusion, so care must be taken to avoid this as the resulting mechanical properties will be severely diminished.
Nickel Element. Nickel is a strong austenite stabilizer. Nickel can prevent transformations and carbide precipitation even at reduced cooling rates during quenching. This can make a nickel a useful addition in products that have heavy section sizes. Increasing nickel content is associated with increased toughness, a slight drop in tensile strength and has no effect on the yield strength. Nickel is also used in welding filler materials for manganese steels to allow the as-deposited material to be free from carbides. It is typical to have lower carbon levels in these materials along with the elevated nickel to produce the desired result.
Aluminum Element. Aluminum is used to deoxidize manganese steel, which can prevent pinhole and other gas defects. It is typical to use additions of 3lbs/ton in the ladle. Increasing aluminum contents decreases the mechanical properties of manganese steel while increasing brittleness and hot tearing. In practice, it is advisable to keep aluminum residuals fairly low for most grades of manganese steel.
Titanium Element. Titanium can be used to deoxidize the manganese steel. In addition, titanium can tie up nitrogen gas in titanium nitrides. These nitrides are stable compounds at steelmaking temperatures. Once tied up the nitrogen is no longer available to cause pin holing in the castings. Titanium can also be used to refine the grain size, but the effect is minimal in heavier sections.