Eine autogene Mühle ist eine neue Art von Mahlanlage mit sowohl Brech- als auch Mahlfunktion. Es nutzt das Mahlgut selbst als Medium, um durch die gegenseitige Aufprall- und Mahlwirkung eine Zerkleinerung zu erreichen. Die halbautogene Mühle soll eine kleine Anzahl von Stahlkugeln in die autogene Mühle aufnehmen, ihre Verarbeitungskapazität kann um 10 – 30 % erhöht werden, der Energieverbrauch pro Produkteinheit kann um 10 – 20 % gesenkt werden, aber die Der Linerverschleiß ist relativ um 15% erhöht und die Produktfeinheit ist gröber. Als wesentlicher Bestandteil der halbautogenen Mühle werden die Mantelbuchsen des Zylinderkörpers durch den Aufprall der vom Liner-Hubbalken angehobenen Stahlkugel auf den Liner am anderen Ende während des Betriebs der SAG-Mühle ernsthaft beschädigt.
2009 wurden zwei neue halbautogene Mühlen mit einem Durchmesser von 7.53 × 4.27 eingebaut Panzhihua Eisen und Stahl Co., Ltd., mit einer jährlichen Konstruktionskapazität von 2 Millionen Tonnen/Set. Im Jahr 2011 wurde im Baima-Konzentrator von Panzhihua Iron and Steel Co., Ltd. eine neue halbautogene Mühle mit einem Durchmesser von 9.15 × 5.03 mit einer jährlichen Auslegungskapazität von 5 Millionen Tonnen gebaut. Seit dem Probebetrieb der halbautogenen Mühle mit einem Durchmesser von 9.15 × 5.03 brechen die Mantelauskleidungen und die Gitterplatte der Mühle oft und die Betriebsrate beträgt nur 55%, was die Produktion und Effizienz stark beeinträchtigt.
In der 9.15 m langen halbautogenen Mühle in der Baima-Mine der Panzhihua Iron and Steel Group wurde die von vielen Herstellern hergestellte Zylinderlaufbuchse verwendet. Die längste Lebensdauer beträgt weniger als 3 Monate und die kürzeste Lebensdauer beträgt nur eine Woche, was zu einem geringen Wirkungsgrad der halbautogenen Mühle und den stark erhöhten Produktionskosten führt. Nanjing Qiming Machinery Co.; GmbH ging tief in das Gelände einer 9.15 m halbautogenen Mühle für kontinuierliche Untersuchungen und Tests. Durch die Optimierung von Gussmaterial, Gussverfahren und Wärmebehandlungsprozess hat die Lebensdauer der in der Baima-Mine hergestellten Shell Liner 4 Monate überschritten, und der Effekt ist offensichtlich.
Ursachenanalyse der kurzen Lebensdauer von SAG-Mühlenschalenauskleidungen
Die Parameter und die Struktur der halbautogenen Mühle φ 9.15 × 5.03 im Baima-Konzentrator. Tabelle 1 ist die Parametertabelle:
Artikel | Datum | Artikel | Datum | Artikel | Datum |
Zylinderdurchmesser (mm) | 9150 | Effektives Volumen (M3) | 322 | Materialgröße | ≤ 300 |
Zylinderlänge (mm) | 5030 | Durchmesser der Stahlkugel (mm) | <150 | Designkapazität | 5 Millionen Tonnen / Jahr |
Motorleistung (KW) | 2*4200 | Ballfüllrate | 8 % ~ 12 % | Umgang mit Materialien | V-Ti-Magnetit |
Geschwindigkeit (U / min) | 10.6 | Materialfüllrate | 45% ~ 55% | Mühlenauskleidungsmaterial | Alloy Steel |
Fehleranalyse der alten SAG-Mühlenschalenauskleidungen
Seit der Inbetriebnahme der halbautogenen Mühle φ 9.15 × 5.03 im Baima-Konzentrator beträgt die Betriebsrate aufgrund der unregelmäßigen Beschädigung und des Austauschs von Mühlenauskleidungen nur etwa 55%, was die wirtschaftlichen Vorteile erheblich beeinträchtigt. Der Hauptversagensmodus der Schalenauskleidung ist in Fig. 1 (a) gezeigt. Gemäß der Vor-Ort-Untersuchung sind die SAG-Mühlenschalenauskleidungen und die Gitterplatte die Hauptfehlerteile, die mit der Situation in Fig. 2 (b) übereinstimmen. Wir schließen andere Faktoren nur von der Analyse des Liners selbst aus. Die Hauptprobleme sind folgende:
1. Aufgrund der falschen Materialauswahl verformt sich die Auskleidungsplatte des Zylinders im Verlauf des Gebrauchs, was zur gegenseitigen Extrusion der Auskleidungsplatte führt, was zu Bruch und Ausschuss führt.
2. Als Hauptbestandteil der Zylinderlaufbuchse nimmt aufgrund der mangelnden Verschleißfestigkeit bei einer Laufbuchsenstärke von etwa 30 mm die Gesamtfestigkeit des Gussstücks ab, und der Aufprall der Stahlkugel kann nicht widerstanden werden, was zu Bruch und Bruch führt Verschrottung;
3. Gussqualitätsmängel wie Verunreinigungen in geschmolzenem Stahl, hoher Gasgehalt und nicht kompakte Struktur verringern die Festigkeit und Zähigkeit von Gussteilen.
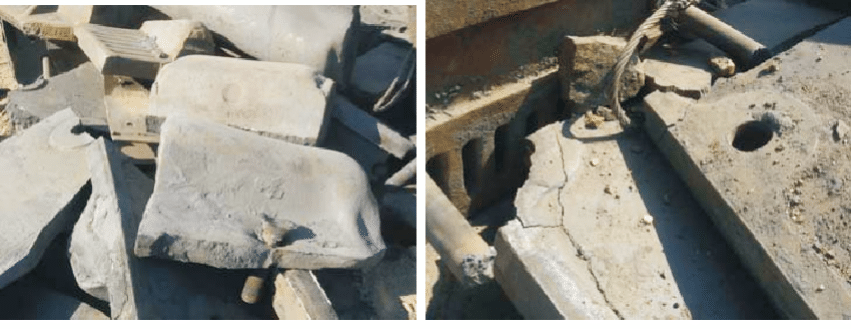
Abb. 1 Hauptfehlermodi von Shell-Liner
Neues Materialdesign von SAG Mill Shell Liner
Das Prinzip der Auswahl der chemischen Zusammensetzung besteht darin, dass die mechanischen Eigenschaften der Schalenauskleidung und der Gitterplatte die folgenden Anforderungen erfüllen:
1) Hohe Verschleißfestigkeit. Der Verschleiß der Schalenauskleidung und der Gitterplatte ist der Hauptfaktor, der zu einer Verringerung der Lebensdauer der Schalenauskleidung führt, und die Verschleißfestigkeit repräsentiert die Lebensdauer der Schalenauskleidung und der Gitterplatte.
2) Hohe Schlagzähigkeit. Die Schlagzähigkeit ist eine Eigenschaft, die den ursprünglichen Zustand wiederherstellen kann, nachdem bestimmte äußere Kräfte sofort aufgebracht wurden. Damit die Schalenauskleidung und die Gitterplatte beim Aufprall der Stahlkugel nicht reißen.
Chemische Zusammensetzung
1) Der Gehalt an Kohlenstoff und C wird unter verschiedenen Verschleißbedingungen, insbesondere der Stoßbelastung, zwischen 0.4% und 0.6% geregelt.
2) Die Ergebnisse zeigen, dass der Gehalt an Si und Si Ferrit stärkt, das Fließverhältnis erhöht, die Zähigkeit und Plastizität verringert und die Tendenz hat, die Sprödigkeit des Temperaments zu erhöhen, und der Gehalt zwischen 0.2 und 0.45% kontrolliert wird;
3) Mn-Gehalt, Mn-Element spielt hauptsächlich die Rolle der Lösungsverstärkung, Verbesserung der Festigkeit, Härte und Verschleißfestigkeit, Erhöhung der Sprödigkeit des Temperaments und der Vergröberungsstruktur, und der Gehalt wird zwischen 0.8 und 2.0% kontrolliert;
4) Chromgehalt, Cr-Element, ein wichtiges Element von verschleißfestem Stahl, hat eine große Verstärkungswirkung auf den Stahl und kann die Festigkeit, Härte und Verschleißfestigkeit des Stahls verbessern, und der Gehalt wird zwischen 1.4 und 3.0% kontrolliert;
5) Mo-Gehalt, Mo-Element ist eines der Hauptelemente von verschleißfestem Stahl, verstärkt Ferrit, verfeinert Korn, verringert oder beseitigt die Sprödigkeit des Temperaments, verbessert die Festigkeit und Härte von Stahl, der Gehalt wird zwischen 0.4 und 1.0% kontrolliert;
6) Der Gehalt an Ni wird innerhalb von 0.9 bis 2.0% kontrolliert.
7) Wenn der Vanadiumgehalt gering ist, wird die Korngröße verfeinert und die Zähigkeit verbessert. Der Vanadiumgehalt kann innerhalb von 0.03 bis 0.08% kontrolliert werden;
8) Die Ergebnisse zeigen, dass der Desoxidations- und Kornverfeinerungseffekt von Titan offensichtlich ist und der Gehalt zwischen 0.03% und 0.08% kontrolliert wird;
9) Re kann geschmolzenen Stahl reinigen, die Mikrostruktur verfeinern, den Gasgehalt und andere schädliche Elemente in Stahl reduzieren. Die Festigkeit, Plastizität und Ermüdungsbeständigkeit von Hochstahl kann innerhalb von 0.04 bis 0.08% kontrolliert werden;
10) Der Gehalt an P und s sollte unter 0.03% kontrolliert werden.
Die chemische Zusammensetzung der neuen SAG-Mühlenschalenauskleidungen lautet also:
Die chemische Zusammensetzung neuer SAG Mill Shell Shell Liner | |||||||||||
Element | C | Si | Mn | P | S | Cr | Ni | Mo | V | Ti | Re |
Inhalt (%) | 0.4-0.6 | 0.2-0.45 | 0.8-2.0 | 0. 03 | 0. 03 | 1.4-3.0 | 0.9-2.0 | 0.4-1.0 | Spur | Spur | Spur |
Gießtechnik
Schlüsselpunkte der Gusstechnologie
- Selbsthärtender Kohlendioxid-Natriumsilikat-Sand wird verwendet, um den Feuchtigkeitsgehalt von Formsand streng zu kontrollieren.
- Es ist eine reine Zirkonpulverbeschichtung auf Alkoholbasis zu verwenden, und abgelaufene Produkte dürfen nicht verwendet werden.
- Unter Verwendung von Schaumstoff zur Herstellung der gesamten festen Probe muss jedes Gussfilet auf dem Körper herausgebracht werden, wobei die genaue Größe und die angemessene Struktur erforderlich sind.
- Während des Formprozesses sollte die Verformung streng kontrolliert werden und der Bediener sollte den Sand gleichmäßig einbringen, und die Sandform sollte kompakt genug und gleichmäßig sein, und gleichzeitig sollte die Verformung der realen Probe vermieden werden.
- Bei der Formmodifikation sollte die Größe streng überprüft werden, um die Maßgenauigkeit der Sandform sicherzustellen.
- Die Sandform muss vor dem Schließen der Box getrocknet werden.
- Überprüfen Sie die Größe jedes Kerns, um eine ungleichmäßige Wandstärke zu vermeiden.
Angusssystem und Steigrohr
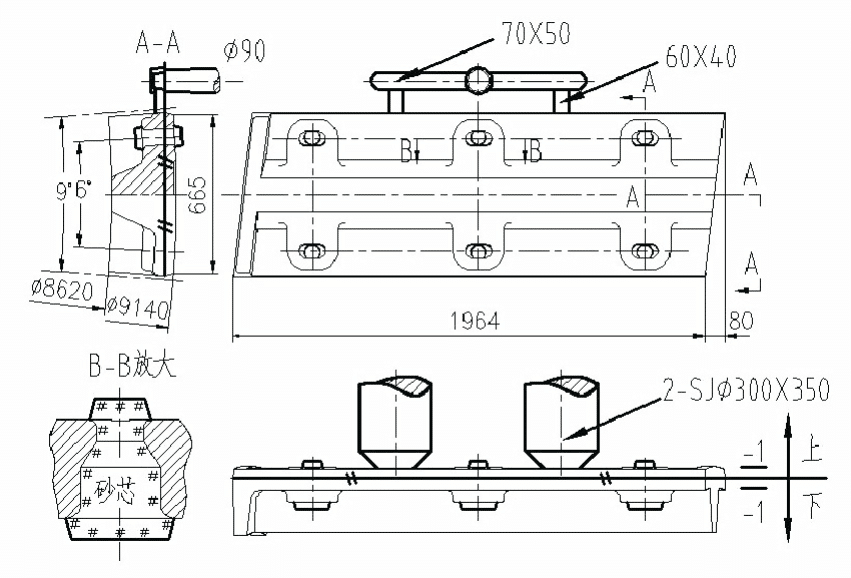
Abb. 2 Gießprozessdiagramm von Schalenauskleidungen
Auswahlprozess
Die Gießtemperatur ist der Hauptfaktor, der die innere Struktur von Gussteilen beeinflusst. Wenn die Gießtemperatur zu hoch ist, die überhitzte Wärme der Stahlschmelze groß ist, kann der Guss leicht eine Schrumpfporosität und eine grobe Struktur erzeugen; Wenn die Gießtemperatur zu niedrig ist, ist die überhitzte Wärme von flüssigem Stahl gering und das Gießen nicht ausreichend. Die Gießtemperatur wird zwischen 1510 ° C und 1520 ° C geregelt, was eine gute Mikrostruktur und eine vollständige Befüllung gewährleisten kann. Die richtige Gießgeschwindigkeit ist der Schlüssel für die kompakte Struktur und keinen Schrumpfhohlraum im Steigrohr. Wenn die Gießgeschwindigkeit nahe an der Position der Kühlwasserleitung liegt, ist das Prinzip „zuerst langsam, dann schnell und dann langsam“ zu befolgen. Das heißt, langsam zu gießen. Wenn der geschmolzene Stahl in den Gusskörper eintritt, wird die Gießgeschwindigkeit erhöht, damit der geschmolzene Stahl schnell zum Steigrohr aufsteigt, und dann ist das Gießen langsam. Wenn der geschmolzene Stahl 2/3 der Steigrohrhöhe erreicht, wird das Gießen verwendet, um das Gießen bis zum Ende des Gießens zu bilden.
Wärmebehandlung
Das richtige Legieren von Baustählen mit mittlerem und niedrigem Kohlenstoffgehalt kann die Perlitumwandlung erheblich verzögern und die Bainitumwandlung hervorheben, so dass die von Bainit dominierte Struktur nach dem Austenitisieren, das als bainitischer Stahl bezeichnet wird, in einem großen Bereich kontinuierlicher Abkühlgeschwindigkeit erhalten werden kann. Bainitischer Stahl kann umfassendere Eigenschaften mit einer geringeren Abkühlrate erzielen, wodurch der Wärmebehandlungsprozess vereinfacht und die Verformung verringert wird.
Isotherme Behandlung
Auf dem Gebiet der Eisen- und Stahlmetallurgie ist es eine große Errungenschaft, Bainitstahlmaterialien durch isotherme Behandlung zu erhalten, was eine der Richtungen bei der Entwicklung von Superstahl- und Nanostahlmaterialien darstellt. Austempering-Prozesse und -Ausrüstungen sind jedoch komplex, der Energieverbrauch ist hoch, die Produktkosten sind hoch, die Umwelt mit mittlerer Verschmutzung wird gelöscht, der Produktionszyklus ist lang und so weiter
Luftkühlungsbehandlung
Um die Mängel der isothermen Behandlung zu überwinden, wurde nach dem Gießen durch Luftkühlung eine Art bainitischer Stahl hergestellt. Um jedoch mehr Bainit zu erhalten, müssen Kupfer, Molybdän, Nickel und andere wertvolle Legierungen zugesetzt werden, was nicht nur hohe Kosten, sondern auch eine geringe Zähigkeit aufweist.
Kontrollierte Kühlbehandlung
Die kontrollierte Kühlung war ursprünglich ein Konzept im Prozess des stahlgesteuerten Walzens. In den letzten Jahren hat es sich zu einer effizienten und energiesparenden Wärmebehandlungsmethode entwickelt. Während der Wärmebehandlung kann die entworfene Mikrostruktur erhalten werden und die Eigenschaften von Stahl können durch kontrolliertes Abkühlen verbessert werden. Die Forschung zum kontrollierten Walzen und Kühlen von Stahl zeigt, dass kontrolliertes Kühlen die Bildung von starkem und zähem kohlenstoffarmem Bainit fördern kann, wenn die chemische Zusammensetzung von Stahl geeignet ist. Die üblicherweise verwendeten Verfahren zur kontrollierten Kühlung umfassen Druckstrahlkühlung, laminare Kühlung, Wasservorhangkühlung, Zerstäubungskühlung, Sprühkühlung, turbulente Plattenkühlung, Wasser-Luft-Sprühkühlung und direktes Abschrecken usw. Üblicherweise werden 8 Arten von Steuerkühlungsverfahren verwendet .
Wärmebehandlungsverfahren
Je nach Ausstattungsstatus und tatsächlichen Bedingungen des Unternehmens wenden wir eine kontinuierliche Kühlwärmebehandlungsmethode an. Das spezielle Verfahren besteht darin, die Heiztemperatur entsprechend einer bestimmten Heizrate um AC3 + (50 ~ 100) Celsius zu erhöhen und die Abkühlung zu beschleunigen, indem das von unserer Firma entwickelte Wasser-Luft-Sprühkühlgerät verwendet wird, damit das Material luftgekühlt und luftgekühlt wird selbstgehärtet. Es kann eine vollständige und homogene Bainitstruktur erhalten, eine hervorragende Leistung erzielen, die offensichtlich denselben Produkten überlegen ist, und zweite Arten von Temperversprödigkeit beseitigen.
Die Ergebnisse
- Metallographische Struktur: 6.5 Grad Korngröße
- HRC 45-50
- Die Schalenauskleidung der großen halbautogenen Mühle, die von unserem Unternehmen hergestellt wird, wird seit fast 3.5 Jahren in der 9.15 m langen halbautogenen Mühle in der Baima-Mine der Panzhihua Iron and Steel Group Co., Ltd. eingesetzt. Die Lebensdauer beträgt mehr als 4 Monate und die längste Lebensdauer beträgt 7 Monate. Mit der Erhöhung der Lebensdauer werden die Schleifkosten pro Einheit stark reduziert, die Häufigkeit des Austauschs der Auskleidungsplatte wird stark reduziert, die Produktionseffizienz wird erheblich verbessert und der Vorteil liegt auf der Hand.
- Die Materialauswahl ist der Schlüssel zur Verbesserung der Lebensdauer des Mühlenauskleidungen der großen halbautogenen Mühle und das Legieren von Stahlsorten ist ein wirksamer Weg, um die Verschleißfestigkeit zu verbessern.
- Die Bainitstruktur mit hoher Festigkeit und hoher Zähigkeit ist die Garantie für die Verbesserung der Lebensdauer der Schalenauskleidung der halbautogenen Mühle.
- Der Gießprozess und der Wärmebehandlungsprozess sind perfekt, um sicherzustellen, dass die Gussstruktur dicht ist, was die Lebensdauer der halbautogenen Mühlenschalenauskleidung effektiv verbessern kann.