Unterschiedliche Elemente haben unterschiedliche Funktionen und Wirkungen in den Verschleißteilen aus Manganstahl.
Kohlenstoffelement. Kohlenstoff ist neben Mangan eines der beiden wichtigsten Elemente in Manganstählen. Manganstähle sind eine übersättigte Kohlenstofflösung. Für die meisten Standard-Manganstahlsorten liegen Kohlenstoff und Mangan in einem ungefähren Verhältnis von Mn / C = 10 vor. Diese Stähle haben daher typischerweise 12% Mn und 1.2% C. Dieses Verhältnis wurde hauptsächlich durch frühe Einschränkungen bei der Stahlherstellung festgelegt, und das feste Verhältnis hat keine wirkliche Bedeutung. Das Erhöhen des Kohlenstoffgehalts erhöht die Streckgrenze und verringert die Duktilität. Das folgende Bild zeigt die Auswirkungen einer Erhöhung des Kohlenstoffgehalts auf die Eigenschaften von 13% Manganstahl.
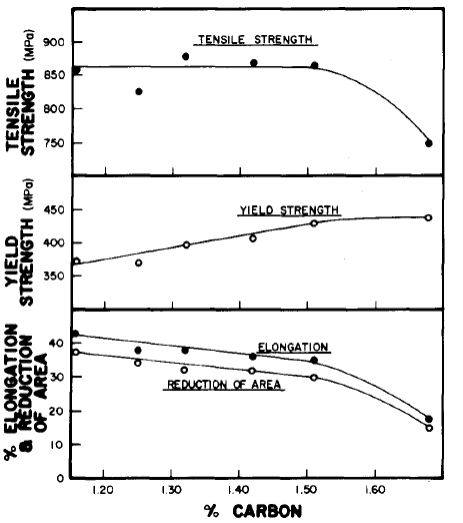
Einfluss von Kohlenstoff auf die Zugeigenschaften von Manganstahl
Die meisten Manganstähle werden zum Ausstechen von Abrieb und bei starkem Verschleiß verwendet, daher versuchen die Hersteller, den Kohlenstoffgehalt zu maximieren. Es gibt praktische Grenzen, und wenn der Kohlenstoffgehalt 1.3% überschreitet, treten Risse und ungelöste Korngrenzencarbide häufiger auf. Die Premium-Qualitäten von Manganstählen mit hohem Mangangehalt haben die obere Kohlenstoffgrenze weit über 1.3% hinausgeschoben.
Manganelement. Mangan ist ein Austenitstabilisator und ermöglicht diese Legierungsfamilie. Es verringert die Umwandlungstemperatur von Austenit zu Ferrit und hilft daher, eine vollständig austenitische Struktur bei Raumtemperatur beizubehalten. Legierungen mit 13% Mn und 1.1% C haben Martensit-Starttemperaturen unter -328 ° F. Die Untergrenze für den Mangangehalt in einfachem austenitischem Manganstahl liegt nahe 10%. Steigende Mangangehalte erhöhen tendenziell die Löslichkeit von Stickstoff und Wasserstoff im Stahl. Premiumlegierungen mit höherem Kohlenstoffgehalt und zusätzlichen Legierungselementen existieren mit Mangangehalten von 16-25% Mangan. Diese Legierungen sind Eigentum ihres Herstellers.
Silikonelement. Der Spezifikationsgehalt von Silizium in Stahl mit hohem Mangangehalt beträgt 0.3% ~ 0.8%. Silizium verringert die Löslichkeit von Kohlenstoff in Austenit, fördert die Karbidausfällung und verringert die Verschleißfestigkeit und Schlagzähigkeit von Stahl. Daher sollte der Siliziumgehalt an der unteren Spezifikationsgrenze kontrolliert werden.
Phosphorelement. Der Spezifikationsgehalt von Stahl mit hohem Mangangehalt beträgt P ≤ 0.7%. Beim Schmelzen von Stahl mit hohem Mangangehalt ist der Phosphorgehalt in Stahl aufgrund des hohen Phosphorgehalts in Ferromangan im Allgemeinen hoch. Da Phosphor die Schlagzähigkeit von Stahl verringert und das Gießen des Gussstücks leicht macht, sollte der Phosphorgehalt von Stahl so weit wie möglich verringert werden.
Schwefelelement. Die Spezifikation von Stahl mit hohem Mangangehalt erfordert S ≤ 0.05%. Aufgrund des hohen Mangangehalts verbinden sich der größte Teil des Schwefels und des Mangans im Stahl zu Mangansulfid (MNS) und gelangen in die Schlacke. Daher ist der Schwefelgehalt im Stahl häufig niedrig (im Allgemeinen nicht mehr als 0.03%). Daher ist die schädliche Wirkung von Schwefel in Stahl mit hohem Mangangehalt höher als die von Phosphor.
Chromelement. Chrom wird verwendet, um die Zugfestigkeit und den Fließwiderstand von Manganstählen zu erhöhen. Zugaben von bis zu 3.0% werden häufig verwendet. Chrom erhöht die lösungsgeglühte Härte und verringert die Zähigkeit des Manganstahls. Chrom erhöht weder die maximale Kalthärte noch die Kaltverfestigungsrate. Chromhaltige Typen erfordern höhere Wärmebehandlungstemperaturen, da Chromcarbide schwieriger in Lösung zu lösen sind. In einigen Anwendungen kann Chrom vorteilhaft sein, aber in vielen Anwendungen ist die Zugabe von Chrom zu Manganstahl nicht vorteilhaft.
Molybdänelement. Molybdänzusätze zu Manganstählen führen zu mehreren Veränderungen. Zunächst wird die Martensit-Starttemperatur gesenkt, wodurch der Austenit weiter stabilisiert und die Karbidausfällung verzögert wird. Als nächstes ändern Molybdänzusätze die Morphologie der Carbide, die sich beim Wiedererhitzen bilden, nachdem das Material eine Lösungsbehandlung erfahren hat. Korngrenzenfilme aus nadelförmigen Carbiden bilden sich typischerweise, aber nach Zugabe von Molybdän werden die ausfallenden Carbide zusammengeschmolzen und durch die Körner verteilt. Das Ergebnis dieser Änderungen ist, dass die Zähigkeit des Stahls durch Zugabe von Molybdän verbessert wird. Ein weiterer Vorteil von Molybdänzusätzen können die mechanischen Eigenschaften im Gusszustand verbessert werden. Dies kann ein echter Vorteil bei der Gussproduktion sein. Bei höheren Kohlenstoffqualitäten erhöht Molybdän die Tendenz zur beginnenden Fusion. Daher muss darauf geachtet werden, dies zu vermeiden, da die resultierenden mechanischen Eigenschaften stark beeinträchtigt werden.
Nickelelement. Nickel ist ein starker Austenitstabilisator. Nickel kann Umwandlungen und Karbidausfällungen auch bei verringerten Abkühlraten während des Abschreckens verhindern. Dies kann Nickel zu einer nützlichen Ergänzung bei Produkten mit schweren Querschnittsgrößen machen. Ein zunehmender Nickelgehalt ist mit einer erhöhten Zähigkeit, einem leichten Abfall der Zugfestigkeit verbunden und hat keinen Einfluss auf die Streckgrenze. Nickel wird auch zum Schweißen von Füllstoffen für Manganstähle verwendet, damit das abgeschiedene Material frei von Karbiden ist. Es ist typisch, dass diese Materialien zusammen mit dem erhöhten Nickelgehalt einen niedrigeren Kohlenstoffgehalt aufweisen, um das gewünschte Ergebnis zu erzielen.
Aluminiumelement. Aluminium wird zur Desoxidation von Manganstahl verwendet, wodurch Loch- und andere Gasdefekte vermieden werden können. Es ist typisch, Zugaben von 3 Pfund / Tonne in der Pfanne zu verwenden. Eine Erhöhung des Aluminiumgehalts verringert die mechanischen Eigenschaften von Manganstahl, während die Sprödigkeit und das Heißreißen erhöht werden. In der Praxis ist es ratsam, die Aluminiumrückstände für die meisten Manganstahlsorten relativ niedrig zu halten.
Titanelement. Titan kann zum Desoxidieren des Manganstahls verwendet werden. Darüber hinaus kann Titan Stickstoffgas in Titannitriden binden. Diese Nitride sind bei Stahlerzeugungstemperaturen stabile Verbindungen. Nach dem Zusammenbinden steht der Stickstoff nicht mehr zur Verfügung, um ein Loch in den Gussteilen zu verursachen. Titan kann auch verwendet werden, um die Korngröße zu verfeinern, aber der Effekt ist in schwereren Abschnitten minimal.