Různé prvky mají různé funkce a účinky v opotřebitelných částech odlévání z manganové oceli.
Uhlíkový prvek. Uhlík je jedním z dvou nejdůležitějších prvků v manganových ocelích spolu s manganem. Manganové oceli jsou přesyceným roztokem uhlíku. U většiny standardních druhů manganové oceli jsou uhlík a mangan v přibližném poměru Mn / C = 10. Tyto oceli proto obvykle mají 12% Mn a 1.2% C. Tento poměr byl stanoven hlavně časnými omezeními výroby oceli a stálý poměr nemá žádný skutečný význam. Zvýšení obsahu uhlíku zvyšuje mez kluzu a snižuje tažnost. Následující obrázek ukazuje účinky zvýšení obsahu uhlíku na vlastnosti 13% manganové oceli.
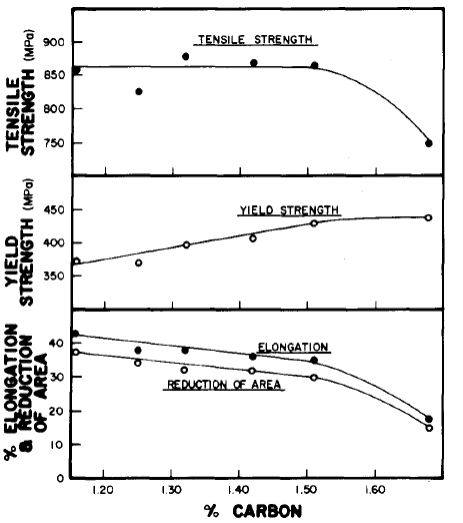
Vliv uhlíku na tahové vlastnosti manganové oceli
Většina manganových ocelí se používá při oděru drážkování a při vysokém rázovém opotřebení, takže se výrobci snaží maximalizovat obsah uhlíku. Praktické limity skutečně existují a jelikož obsah uhlíku překračuje 1.3%, dochází k praskání a stále častěji se vyskytují nerozpuštěné karbidy hranic zrn. Prémiové třídy manganových ocelí, ty s vysokým obsahem manganu, posunuly horní mez uhlíku výrazně nad 1.3%.
Manganový prvek. Mangan je stabilizátor austenitu a umožňuje tuto rodinu slitin. Snižuje teplotu transformace austenitu na ferit, a proto pomáhá udržovat plně austenitickou strukturu při pokojové teplotě. Slitiny s 13% Mn a 1.1% C mají počáteční teploty martenzitu pod -328 ° F. Dolní hranice obsahu manganu v čisté austenitické manganové oceli je téměř 10%. Zvyšující se hladiny manganu mají tendenci zvyšovat rozpustnost dusíku a vodíku v oceli. Prémiové slitiny s vyšším obsahem uhlíku a dalšími prvky slitiny existují s obsahem manganu od 16 do 25% manganu. Tyto slitiny jsou vlastnictvím jejich výrobce.
Silikonový prvek. Specifikační obsah křemíku v oceli s vysokým obsahem manganu je 0.3% ~ 0.8%. Křemík sníží rozpustnost uhlíku v austenitu, podpoří srážení karbidů a sníží odolnost proti opotřebení a rázovou houževnatost oceli. Proto by měl být obsah křemíku řízen na spodní mezní specifikaci.
Fosforový prvek. Specifikační obsah oceli s vysokým obsahem manganu je P ≤ 0.7%. Při tavení oceli s vysokým obsahem manganu je obsah fosforu v oceli kvůli vysokému obsahu fosforu v feromanganu obecně vysoký. Vzhledem k tomu, že fosfor sníží rázovou houževnatost oceli a usnadní odlití odlitku, měl by být obsah fosforu v oceli co nejvíce snížen.
Sírový prvek. Specifikace oceli s vysokým obsahem manganu vyžaduje S ≤ 0.05%. Vzhledem k vysokému obsahu manganu se většina síry a manganu v oceli navzájem spojuje a vytváří sirník manganatý (MNS) a vstupuje do strusky. Proto je obsah síry v oceli často nízký (obvykle ne více než 0.03%). Proto je škodlivý účinek síry v oceli s vysokým obsahem manganu vyšší než ve fosforu.
Chromový prvek. Chrom se používá ke zvýšení pevnosti v tahu a odolnosti proti toku u manganových ocelí. Často se používají přírůstky až 3.0%. Chrom zvyšuje tvrdost žíhání v roztoku a snižuje houževnatost manganové oceli. Chrom nezvyšuje maximální úroveň tvrdosti zpevněnou tvrdostí ani rychlost zpevnění. Jakost obsahující chrom vyžaduje vyšší teploty tepelného zpracování, protože karbidy chromu se obtížněji rozpouštějí v roztoku. V některých aplikacích může být chrom přínosný, ale v mnoha aplikacích není přínosem přidání chromu do manganové oceli.
Prvek molybdenu. Přídavek molybdenu do manganových ocelí má za následek několik změn. Nejprve se sníží teplota startu martenzitu, což dále stabilizuje austenit a zpomalí srážení karbidu. Přídavky molybdenu dále mění morfologii karbidů, které se tvoří během opětovného zahřívání poté, co byl materiál podroben ošetření roztokem. Typicky se tvoří hraniční filmy aikulárních karbidů, ale po přidání molybdenu se karbidy, které se vysráží, spojí a rozptýlí se v zrnech. Výsledkem těchto změn je, že houževnatost oceli se zvyšuje přidáním molybdenu. Další výhodou přídavků molybdenu mohou být vylepšené mechanické vlastnosti odlitku. To může být skutečnou výhodou během výroby odlévání. U vyšších tříd uhlíku bude molybden zvyšovat tendenci k počáteční fúzi, proto je třeba dbát na to, aby se tomu zabránilo, protože výsledné mechanické vlastnosti budou vážně sníženy.
Niklový prvek. Nikl je silný stabilizátor austenitu. Nikl může zabránit transformacím a srážení karbidů i při snížené rychlosti ochlazování během kalení. Díky tomu může být nikl užitečným doplňkem u produktů, které mají velké části. Zvýšení obsahu niklu je spojeno se zvýšenou houževnatostí, mírným poklesem pevnosti v tahu a nemá žádný vliv na mez kluzu. Nikl se také používá při svařování přídavných materiálů pro manganové oceli, aby se umožnilo, aby uložený materiál neobsahoval karbidy. Pro dosažení požadovaného výsledku je typické mít v těchto materiálech nižší hladinu uhlíku spolu se zvýšeným obsahem niklu.
Hliníkový prvek. Hliník se používá k deoxidaci manganové oceli, což může zabránit defektům v dírkách a jiných plynech. Typické je použít v pánvi přísady 3 libry / tunu. Zvýšení obsahu hliníku snižuje mechanické vlastnosti manganové oceli a současně zvyšuje křehkost a trhání za tepla. V praxi se doporučuje udržovat zbytky hliníku na většině druhů manganové oceli poměrně nízké.
Titanový prvek. Titan lze použít k deoxidaci manganové oceli. Titan může navíc vázat plynný dusík v nitridech titanu. Tyto nitridy jsou stabilní sloučeniny při teplotách výroby oceli. Jakmile je vázán, dusík již není k dispozici, aby způsobil zařezávání kolíků do odlitků. K zjemnění zrna lze také použít titan, ale v těžších úsecích je účinek minimální.